Healthcare facility finds a fresh approach to water treatment at Jaytech
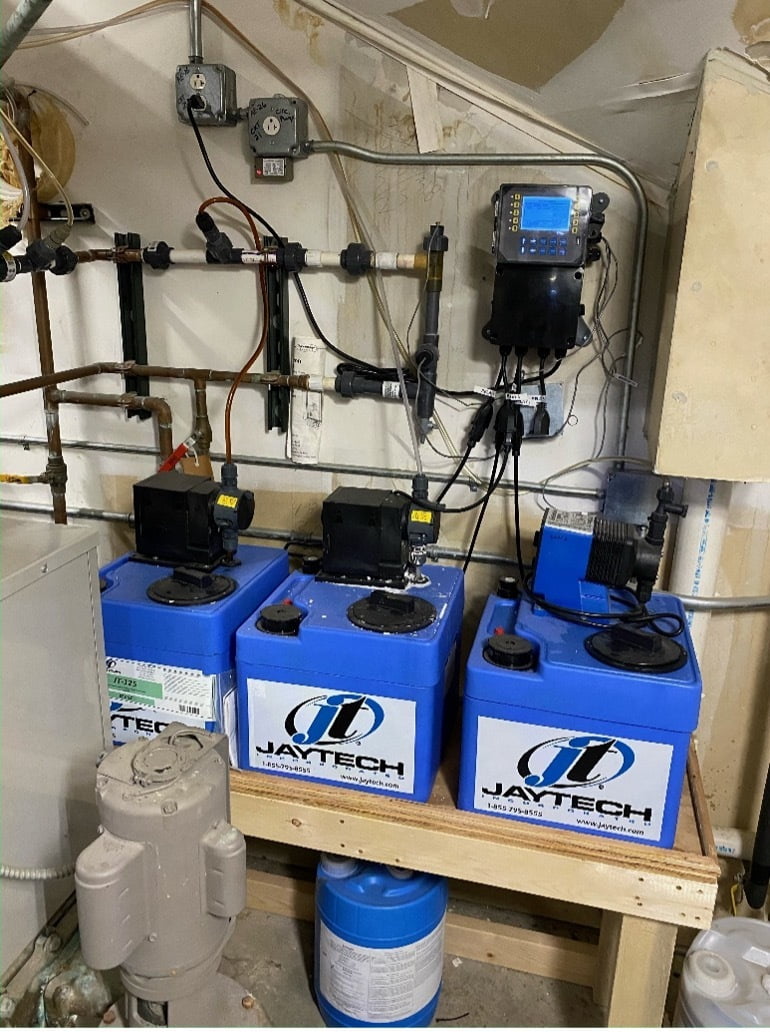
We got the call and found one facility's water treatment from terrible to restored, and we found cost saving options.
Jaytech quickly responded to a customer’s water treatment problem assessed the issue, reported our findings of a poor water treatment program, and got this system back up and running saving money and time. Jaytech successfully halted the corrosion occurring in the heat recovery loop and prevented any future pinhole occurrences in the mild steel piping. Furthermore, the system is now balanced with appropriate chemistries and equipped with proper freeze protection for the winter season. By introducing a hydronic additive, the utility bill was reduced by an average of 17.16%. Since our hydronic additive was added to the heat recovery loop in August 2020, the nursing facility has been able to save an average of $637.79 per month on utilities.
How did we get involved?
In September 2019, Jaytech received a referral from a local mechanical contractor to assist a nursing home facility in the St. Louis area. The facility was experiencing issues with their heat recovery system because of inadequate water treatment by their current vendor. They were noticing premature piping failure in their mild steel base materials or pin hole leaks that were affecting efficiency and operating costs.
What was the issue?
Early investigation revealed mild steel inhibitor was present in adequate concentration for a closed loop. However, the system lacked copper corrosion inhibitor. As a result, the copper corrosion byproduct (soluble copper) levels were higher than 5 ppm, and the soluble iron levels were at 8.2 ppm. These elevated levels were the result of a chain of events: the absence of copper inhibition led to the release of copper corrosion byproducts; mild steel was then copper plated, causing iron corrosion byproducts to be released into the water by means of galvanic corrosion. Lack of knowledge or care from their water treatment company led this customer down an expensive chain of events.
We then proceeded to examine the fluid cooler program. It was observed that the tower had accumulated scale and biological growth from improper feeding, dosing, and control of the water treatment chemistries. Moreover, there was mold growing inside the tank containing the scale/corrosion inhibitor making it ineffective. The current water treatment vendor was only utilizing one biocide, 12.5% sodium hypochlorite, as a biocide program. This primitive water treatment program was inadequate to prevent premature failure in this HVAC system.
How did we solve the issue?
Jaytech utilized a multi-metal cleaner to remove the existing corrosion. It was agreed upon with the customer that the loop would have a flushing performed, then JT-3450 was ran for two weeks. After two weeks the loop was flushed again, then retreated with 30% glycol, corrosion inhibitors, non-oxidizing biocide, and a Jaytech recommended Hydronic Additive. After this clean/flush/retreat procedure, we utilized a more sophisticated water treatment program to meet this customer’s needs. This system needed more regular monitoring and inspections.
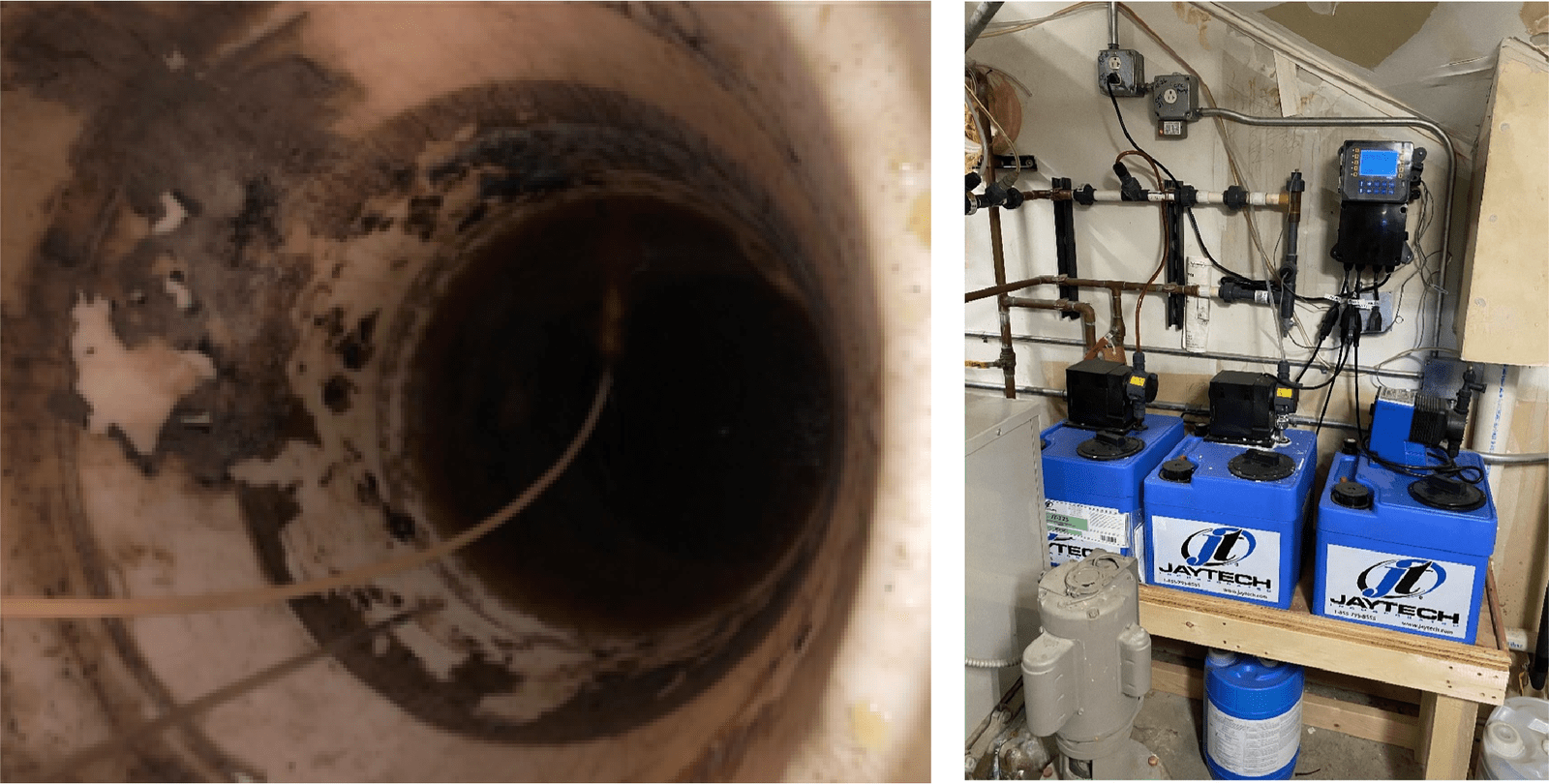
The Fluid Cooler was recommended to have an upgraded chemical program. Instead of the two chemical programs being used where 5-gallon pails were being carried upstairs, it was recommended to the customer to move to a three-pump (dual biocide) program. With the addition of an EPA registered non-oxidizing biocide treatment we also recommended switching to ultra-concentrate liquids to reduce labor and waste on containers.
What did the customer appreciate about our services?
Jaytech quickly responded to a customer’s water treatment problem assessed the issue, reported our findings of a poor water treatment program, and got this system back up and running saving money and time. Jaytech successfully halted the corrosion occurring in the heat recovery loop and prevented any future pinhole occurrences in the mild steel piping. Furthermore, the system is now balanced with appropriate chemistries and equipped with proper freeze protection for the winter season. By introducing a hydronic additive, the utility bill was reduced by an average of 17.16%. Since our recommended Hydronic Additive was added to the heat recovery loop in August 2020, the nursing facility has been able to save an average of $637.79 per month on utilities.
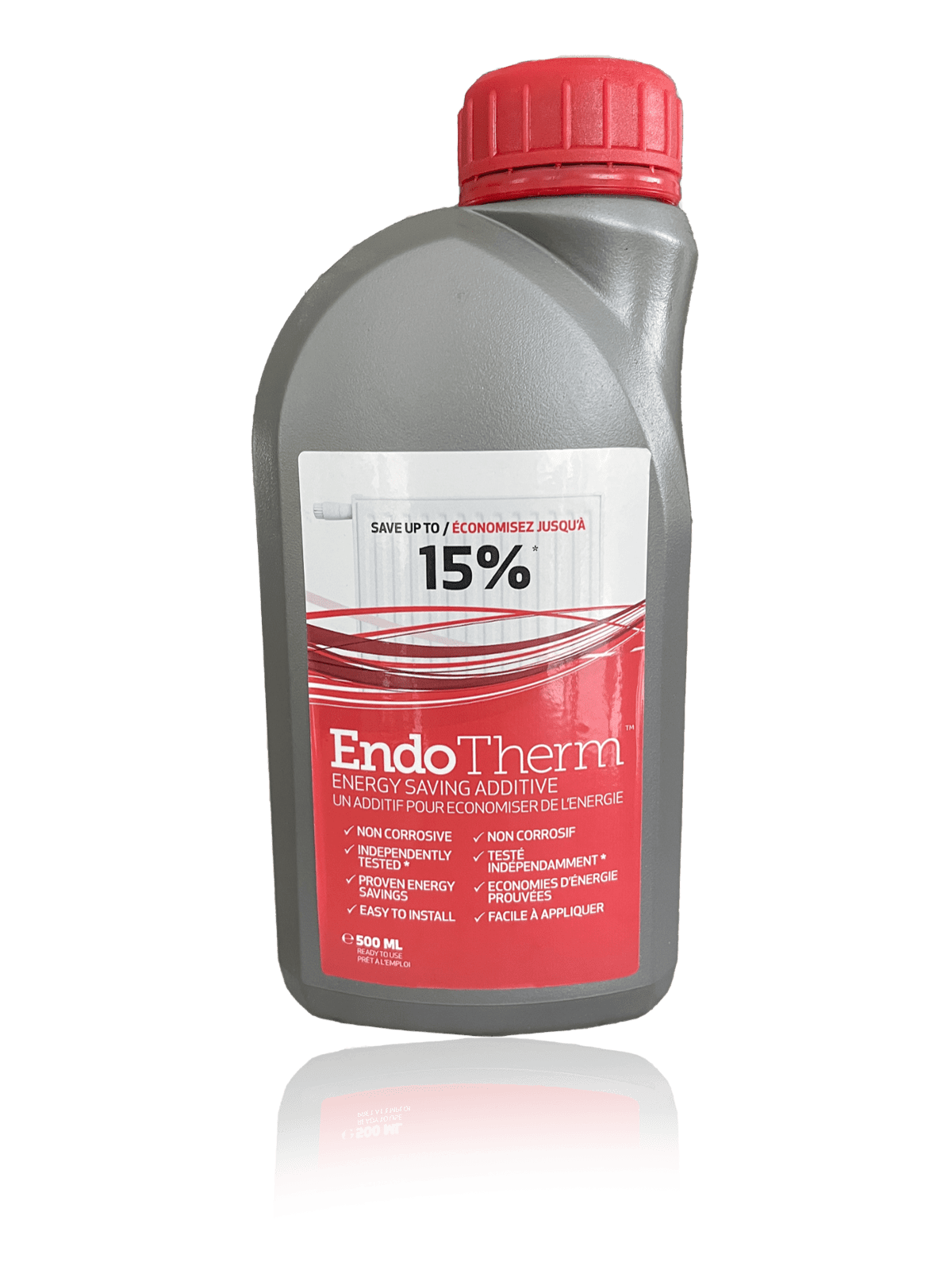
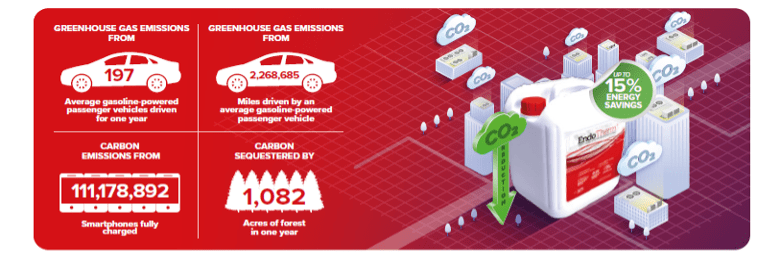